시스템의 복잡성이 날로 높아지고 있고 아키텍처, 파티셔닝, 전원장치, 퓨징, 배선, 컨트롤러 등이 긴밀하게 연관돼 있어 향상된 전력 분배 아키텍처로 가능한 최상의 결과를 달성하도록 하기 위해서는 자동차 업체, 시스템 협력사, 반도체 공급사 사이의 긴밀한 협력이 요구된다. 다임러, 인피니언 등으로 구성된 프로젝트 팀은 가능한 모든 위치에서 해당 컨트롤러의 모든 릴레이 및 퓨즈를 반도체로 교체하고, 프로토타입을 이용해 특히 열 특성, 설치 공간, 비용 측면에서 이 기술의 타당성을 검증했다. 일련의 변형 아키텍처들을 이용해 현실적인 적용 가능성, 효율 향상, 비용 절감 가능성을 평가했다.
글│토비아스 라이델(Tobias Raithel), 다임러
알폰스 그라프(Alfons Graf), 유르겐 코지자(Juergen Kositz), 인피니언
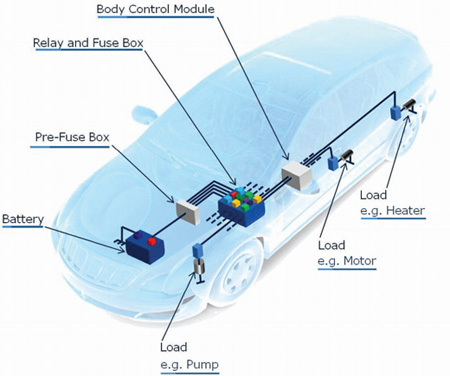
첨단 자동차 전력 분배
아키텍처의 해결 과제
지난 몇 년 사이 자동차 내 부하 수가 급격히 증가하면서 자동차 전력 분배 시스템의 복잡도가 크게 높아졌다. 이와 같은 추가적인 부하들을 스위칭하기 위해서는 현재의 전력 분배기 및 컨트롤러를 확장해야 하는데, 그러기 위해서는 이용 가능한 공간의 제약과 증가하는 열 발생 문제를 극복해야만 한다. 뿐만 아니라 스톱앤스타트(stop & start) 기능과 하이브리드 카 및 전기차가 새로운 과제들을 제기함에 따라 자동차 업체들은 전력 분배 시스템을 재고하지 않을 수 없게 됐다. 특히 전기기계식 전력 분배기를 어떻게 최적화할 수 있을 것인가를 고민하지 않을 수 없게 됐다.
새로운 반도체 기술이 등장함에 따라 특정한 전류 수준의 릴레이를 과거에는 경제성이 떨어지는 솔루션이었던 반도체 스위치로 교체할 수 있게 됐다. 이 방법은 기능성을 향상시킬 수 있을 뿐만 아니라(스위칭 주파수, 펄스 폭 변조, 향상된 진단 등) 전력 손실을 낮출 수 있고, 전력 분배 컨트롤러와 배선 모두의 무게를 낮출 수 있다. 그럼으로써 동일한 또는 더 낮은 시스템 비용으로 CO2 배출을 줄일 수 있다.
뿐만 아니라 지능적 반도체 스위치(인피니언 테크놀로지스의 PROFET™+ 및 Power PROFET™ 제품군 등)를 이용해 릴레이 뿐만 아니라 퓨즈까지도 교체할 수 있다. 이에 따라 전체적인 시스템이 더 우수한 신뢰성을 갖고 동작할 수 있으며 더 이상 유지보수를 필요로 하지도 않는다. 또한 현재로서는 자동차 내에서 접근하거나 활용하기 곤란한 위치에 있는 설치 공간도 새롭게 활용할 수 있는 길이 열렸다.
시스템의 복잡성이 날로 높아지고 있고 아키텍처, 파티셔닝, 전원장치, 퓨징, 배선, 컨트롤러 등이 긴밀하게 연관돼 있어 향상된 전력 분배 아키텍처로 가능한 최상의 결과를 달성하도록 하기 위해서는 자동차 업체, 시스템 협력사, 반도체 공급사 사이의 긴밀한 협력이 요구된다.
이 글에서 설명하는 프로젝트 팀에는 자동차 회사, 전력 분배 시스템 및 배선 협력사, 반도체 공급사 등 3개 파트너사가 참여했다. 이들 세 파트너 모두는 각자 분야의 전문적인 회사들이다. 긴밀한 협력과 활발한 소통이 이 프로젝트가 성공할 수 있었던 원동력이 됐다.
프로젝트는 2년의 기간 동안 진행됐으며 다음과 같은 두 가지 목표를 달성하고자 했다.
- 가능한 모든 위치에서 해당 컨트롤러의 모든 릴레이 및 퓨즈를 반도체로 교체한다. 이 프로토타입을 이용해서 특히 열 특성, 설치 공간, 비용 측면에서 이 기술의 타당성을 검증한다.
- 일련의 변형 아키텍처들을 이용해서 현실적인 적용 가능성, 효율 향상, 비용 절감 가능성을 평가한다.
현행 EE 아키텍처의 분석
프로젝트의 첫 번째 단계는 컨트롤러에 중점을 두고서 현행 EE 아키텍처를 상세히 분석하는 것이었다. 분석 대상 아키텍처는 5개의 컨트롤러를 포함했다. 3개의 전력 분배기는 릴레이 및 퓨즈를 기반으로 한 것이고, 2개의 동체 제어 모듈은 반도체를 기반으로 한 것이었다. 전력 분배기는 릴레이와 퓨즈를 이용해 고전류 부하(에어 서스펜션 컴프레서, 히티드 와이퍼 파크 등)를 스위칭하고 다른 컨트롤러(점화 록 전압, 단자 15 등)로 전력을 공급한다. 작업의 목적은 전력 분배기의 설치 공간, 무게, 전력 손실을 최적화하는 하기 위한 것이었다. 그러기 위해서는 먼저 릴레이와 퓨즈의 전력 소모를 계산해야 했다.
이들 릴레이 및 퓨즈를 반도체 스위치로 교체하고 배선을 최적화하기 위해서는 각각의 모든 전력 소모 요인에 대해 부하 프로파일을 분석해야 했다. 또한 부하를 온으로 스위칭할 때, 극성이 반전될 때, 모터 스톨 등과 같은 단일 결함이 발생했을 때 부하가 어떻게 동작하는지, 그리고 전류를 제로로 정류했을 때(inductive cutoff) 더 높은 에너지를 발생시키는지 알아보기 위해 추가적인 조사가 필요했다. 이러한 분석은 적합한 반도체 스위치를 선택하고 프리휠링 다이오드 등과 같은 추가적인 부품들을 검토하기 위해서 필요했다. 이 분석은 또한 각각의 부하에 대해서 스위칭 주파수, 온 대 오프 시간 비율, 아날로그 액추에이션이 가능하도록 하는 옵션, 전력 전압 강하 특성(콜드 스타트) 등을 결정하기 위해서 필요했다.
이러한 배경 정보를 바탕으로 인피니언은 다음 두 옵션에 이용하기 위한 적합한 반도체 스위치를 선택했다.
- 컨트롤러를 엔진 컴파트먼트에 설치한다.
- 컨트롤러를 패신저 컴파트먼트에 설치한다.
후자의 방법은 주변 온도가 더 낮아 스위치가 더 높은 온도 상승이 허용되므로 비용 최적화 변수로서 더 높은 스위치 저항을 사용할 수 있다.
그 다음 단계로는 전력 분배기 업체가 릴레이와 반도체 스위치 사이의 접합부에 대해서 비용 절감의 가능성을 검토했다. 이 검토는 릴레이 및 반도체 스위치의 순수한 제품 비용을 비교하는 것뿐만 아니라 새로운 시스템을 이용함으로써 전력 손실 감소, 무게 감소, 부피 감소 측면에서 달성되는 비용 절감도 고려했다. 비용 모델을 이용해서 이와 같은 향상을 비용 절감으로 환산할 수 있었으며 자동차 업체에서 무게, 전기 전력 손실, 설치 공간에 해당되는 비용을 제공했다. 배선 업체는 배선을 짧게 또는 가늘게 하고, 커넥터를 단순화하고, 버스 바, 퓨즈, 퓨즈 홀더, 케이블 덕트, 그로밋 등을 제거함으로써 직접적으로 달성할 수 있는 비용 절감의 액수를 제공했다.
프로토타입 컨트롤러
그림 1은 다수의 릴레이를 인피니언 반도체 스위치로 교체한 전자식 전력 분배 컨트롤러 프로토타입을 보여주고 있다. 각각의 부하와 여기에 사용된 스위치는 다음과 같다.
BTS50015-1TAA 및 BTS50045-1TAA는 각기 1.5 mΩ 및 4.5 mΩ 온-상태 저항(실온일 때 최대 값)인 Power PROFET™ 유닛이다. BTC50010-1TAA는 Connect FET으로서 핀을 통해서 병렬로 연결된 자매 트랜지스터인 BTC30010-1TAA를 제어하며 온-상태 저항을 반으로 줄일 수 있도록 한다. BTS5090-1EJA는 PROFET™+ 제품군의 90 mΩ 스위치이다.
그림 1에서는 3개의 릴레이가 교체되지 않고 있다는 것을 알 수 있다. 이렇게 한 이유는 반도체 스위치의 반전 다이오드에서 극성이 반전될 때 역 부하 전류가 발생되는 것을 방지하기 위해다. 이러한 역 전류는 역직렬(antiseries)로 연결된 2개의 반도체 스위치를 이용하거나 또는 정상적으로는 접점을 폐쇄 상태로 유지하고 극성이 역전될 때는 전류 흐름을 차단하는 중앙 릴레이를 이용해서 억제할 수 있다. 스타터 스위치에 탑재된 또 다른 릴레이는 반도체 스위치와 결합해서 중복적인 스위칭 소자로 동작한다. 이와 같이 결합시킴으로써 반도체 스위치가 높은 사이클 수 및 배선 보호를 달성할 수 있으며 릴레이는 중복적인 컷오프 옵션으로서 역 극성 보호를 제공할 수 있다. 이들 릴레이는 직렬로 연결된 정전류 릴레이 드라이버(인피니언의 TLE4247)를 이용해서 구동했다. 그럼으로써 릴레이를 온으로 스위칭할 때는 정상적인 코일 전류를 제공한다. 그리고 일단 릴레이가 에너지화 됐을 때는 이 전류를 필요한 홀딩 값으로 감소시킴으로써 릴레이 코일의 전력 손실을 낮출 수 있다.
이와 같이 반도체 스위치로 전환하기 위해서는 직접적으로 전력 분배기에 탑재된 마이크로컨트롤러를 이용해서 이의 액추에이션 및 진단을 구현해야 한다. 그러기 위해서는 또한 전원장치(TLE4675)와 다른 컨트롤러들과의 CAN 통신(TLE6251DS)을 필요로 한다. 이들 장치들로 인해서 들어가는 추가적인 비용은 릴레이 제어 배선과 그 밖의 진단 피드백 배선 및 그에 따른 커넥터 및 퓨즈를 제거하는 것으로 상쇄할 수 있다.
그런 다음에는 이 전자식 전력 분배 시스템에 대해서 일련의 랩 테스트를 실시했다. 특히 센서와 열 영상 카메라를 이용해서 모듈 및 PCB 온도를 측정하고 기존의 온도 시뮬레이션과 비교했다. 그런 다음 이 전자식 전력 분배 시스템을 수천 킬로미터 테스트 중에 오류를 일으키지 않고 동작한 테스트 자동차에 탑재했다.
그림 2는 레퍼런스 유닛과 새로운 전자식 전력 분배 컨트롤러를 비교해서 보여주고 있다. 새로운 컨트롤러의 크기가 훨씬 작다는 것을 알 수 있다. 따라서 무게 역시 304그램으로 레퍼런스 유닛의 705그램과 비교해 절반에도 미치지 않는다.
아키텍처 분석
아키텍처 분석에서는 현행 레퍼런스 아키텍처와 일련의 변형 아키텍처들을 비교했다. 이들 변형 아키텍처는 컨트롤러의 수 및 위치, 각 부하의 분포가 다르다. 어떤 변형 아키텍처는 위에서 언급한 5개 컨트롤러를 3개로 줄일 수 있었다. 이들 각각의 변형 아키텍처가 배선, 커넥터 콘셉트, 컨트롤러 레이아웃에 대해서 변경을 필요로 했다. 그러므로 이들 옵션의 분석은 순수한 부품 가격뿐만 아니라 이 새로운 시스템과 관련해서 다음과 같은 측면들을 분석하기 위한 것이었다.
- 배선 자재 및 무게에 있어서 비용 절감
- 커넥터, 모듈 하우징, 버스 바, PCB 소재에 있어서 비용 절감
- 퓨즈, 홀더, 릴레이 홀더에 있어서 비용 절감
- 배선 루팅 및 케이블 덕트 변경
- 어셈블리 시퀀스 및 소요 시간의 차이
- 전력 손실, 총 무게, 설치 공간의 감소
그림 3은 레퍼런스 아키텍처와 비교해서 시스템 차원에서 비용 차이를 보여주고 있다. “Basic(기본형)” 및 “High-Level(고급형)”은 자동차 장비 수준을 말한다. 더 높은 수준의 장비일수록 더 많은 비용을 절감할 수 있다는 것을 알 수 있다. 무게 및 전력 손실 감소에 따른 비용 절감을 포함했을 때 가능한 비용 절감이 자동차 한 대당 3~18유로에 이르는 것으로 나타난다.
이와 같이 상당히 고무적인 수준의 비용 절감이 가능하므로 이 솔루션이 향후의 자동차 플랫폼에 채택될 가능성이 높아 보인다.
요약
3개 프로젝트 파트너사 중에 어느 한 회사의 노하우만으로는 이와 같이 복잡한 프로젝트를 성공시킬 수 없었을 것이다. 최상의 결과를 달성하기 위해서는 정보의 활발한 공유가 무엇보다도 필수적으로 요구된다는 것을 알 수 있다.
아키텍처 분석에서는 상당히 높은 수준의 비용 절감이 가능하다는 결론을 얻을 수 있었는데 이것은 프로젝트를 시작할 때 기대했던 것보다 높은 수준이었다. 이 시스템이 여러 측면에서 거둘 수 있는 모든 이점들을 고려했을 때 반도체 기반 전력 분배 컨트롤러는 전기기계식 컨트롤러에 비해서 더 낮은 비용으로 구현할 수 있다는 것을 알 수 있다.
실제적으로 이와 같은 아키텍처 변경은 결코 쉽지 않은 작업으로 단계적이며 점진적으로 시행해 나가야 할 것이다. 이러한 일차적인 단계로서 릴레이 제어 부하를 이미 존재하는 전자식 컨트롤러 위치로 이동시키고 이 부하를 반도체 스위치를 이용해서 구동할 수 있을 것이다. 이렇게 하기 위해서 필요한 배선 변경은 되도록 최소화해야 할 것이다. 하지만 비용 절감의 가능성을 최대한 실현하기 위해서는 새로운 자동차 플랫폼으로 배선과 전력 분배 컨트롤러 아키텍처를 대대적으로 변경해야 할 것이다. AE
AEM(오토모티브일렉트로닉스매거진)
<저작권자 © AEM. 무단전재 및 재배포 금지>